Un mantenimiento adecuado es la clave
Finalizada la estructura metálica, se recomiendan controles de mantenimiento semestrales.
Si es necesario, puede acudir a su ingeniero estructural o contratista para que realice las verificaciones y reparaciones cuando sea necesario.
Mantenimiento de Estructuras y Componentes de Acero
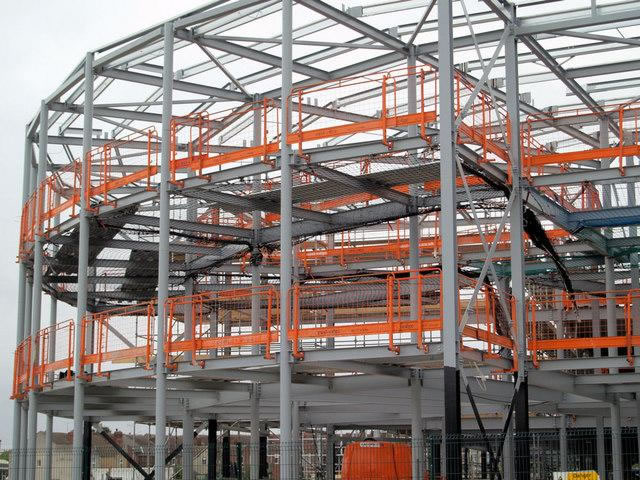
El mantenimiento adecuado es la clave para mejorar la vida útil de la mayoría de las estructuras. Las estructuras de acero son una de ellas. Los fabricantes de metales profesionales ponen su corazón y alma en la creación de mega estructuras, edificios, estructuras marinas magnánimas y estructuras del sector energético de alta tecnología. Una vez producidas, estas estructuras sobreviven durante un largo período de tiempo. La razón es la durabilidad y tenacidad del acero estructural. Pero dicho esto, el uso de estructuras de acero tiene algunas desventajas. Pueden volverse frágiles durante un período de tiempo debido a cambios extremos de temperatura y también son propensos a la corrosión. Para combatir estos inconvenientes, se deben tomar las medidas adecuadas.
Echemos un vistazo a algunos consejos para el mantenimiento de estructuras de acero.
Realizar comprobaciones de mantenimiento
En el caso de los edificios, una vez finalizada la construcción, es recomendable realizar controles de mantenimiento semestrales. Cree un calendario sistemático para estas comprobaciones. Además, asegúrese de realizar controles estacionales después de episodios de condiciones climáticas severas. Si es necesario, pídale a su ingeniero estructural o contratista que realice las verificaciones y realice las reparaciones cuando sea necesario.
Realizar reparaciones menores
Si encuentra agujeros en su estructura de acero o una grieta en la pintura; lo mejor es no dejarlo para el futuro. Nunca se sabe cuándo los problemas menores pueden convertirse en problemas importantes que afectan a la estructura de acero en general. Por lo tanto, rellene todos los agujeros y use imprimación y pintura para reparar los arañazos.
Mantenimiento de Pilotes de Acero
Los pilotes de acero deben mantenerse de vez en cuando. La corrosión puede dañar estas estructuras debilitándolas. El refuerzo de pilotes en H soldando placas de acero en las bridas y el alma es apropiado para las áreas localizadas de corrosión. Existe otro método de refuerzo en el que se sueldan varillas de refuerzo a lo largo del eje principal del miembro reparado a través del área dañada.
Los pilotes de acero pueden requerir protección de recubrimiento o puede haber algunos que requieran protección catódica. Los propios sistemas de protección catódica deben ser inspeccionados en busca de ánodos agotados, conexiones corroídas o sueltas, continuidad eléctrica, etc., y deben ser mantenidos anualmente para asegurar la protección continua del acero.
Pilotes en H
El refuerzo de pilotes en H mediante la soldadura de placas de acero en las bridas y el alma puede ser apropiado en áreas localizadas de corrosión, como la zona de las mareas. Las placas de refuerzo deben tener un espesor suficiente para restaurar la resistencia original del pilote y un área suficiente para abarcar y extenderse más allá de los extremos del área corroída.
El acero viejo debe limpiarse y recortarse hasta un punto en el que el grosor del metal asegure una soldadura fuerte. Todos los bordes cortados deben estar emplumados y la soldadura debe realizarse completamente alrededor de la placa para eliminar las grietas.
Otro método de refuerzo utiliza la encapsulación en hormigón armado. En este método, las varillas de refuerzo se sueldan a lo largo del eje principal del miembro reparado, a través del área dañada. Los lazos se sueldan o atan en todas las intersecciones con acero de refuerzo, se coloca una forma alrededor del pilote y se coloca concreto en el interior.
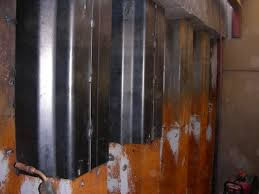
Reparación de pilotes de acero corroídos.
Cuando sea necesario reemplazarlo, el nuevo pilote debe fabricarse con precisión para que coincida con el anterior, asegurándose de que los orificios de los pernos y remaches estén ubicados correctamente. Cuando se reemplazan los pilotes de apoyo, el nuevo pilote generalmente se coloca junto al antiguo en un ligero ángulo. Luego se corta a la altura adecuada, se tapa (generalmente soldando una placa de acero) y se coloca en su posición con un bloque y aparejo.
Si el pilote viejo se retira antes de que se hinque la nueva, la carga debe transferirse temporalmente hasta que el pilote nuevo pueda asumirla.
Tablestacas
Las tablestacas suelen servir como mamparo para retener el relleno. Por lo tanto, se debe tener mucho cuidado durante el reemplazo de uno o más pilotes para evitar fallas y el paso del relleno a través de los espacios abiertos hacia el agua.
Con mayor frecuencia, los agujeros pequeños se reparan soldando placas de acero sobre ellos, y los pilotes muy deteriorados generalmente se reemplazan o protegen colocando nuevos pilotes delante de ellos.
En este último caso, se deben instalar balizas nuevas, tirantes y tiradores, y el espacio entre las pilas nuevas y viejas se debe rellenar con tierra, arena, grava u hormigón bien apisonada. Un método alternativo para reparar pilotes muy deteriorados es instalar un revestimiento de hormigón.
El acero viejo debe limpiarse de óxido, incrustaciones marinas y otros contaminantes antes de instalar una cubierta de concreto de al menos 15cm de espesor. Generalmente se utiliza una forma de madera atornillada para este propósito. Cuando se puede acceder a la parte posterior del mamparo, todo el mamparo de acero se puede revestir con concreto con un espesor mínimo de 7.5cm en cada lado.
Siempre que se reemplace el relleno, debe agregarse en capas (preferiblemente material granular) y estar bien compactado. Para reemplazar las barras de acoplamiento deterioradas, se cava una zanja desde el tablestacado hasta el muerto de concreto, y las nuevas barras con tensores nuevos se instalan una a la vez.
Deben cubrirse con un revestimiento bituminoso, una cinta de tela y un revestimiento bituminoso final. Se debe inspeccionar el muerto de concreto y realizar las reparaciones necesarias antes de rellenar la zanja.
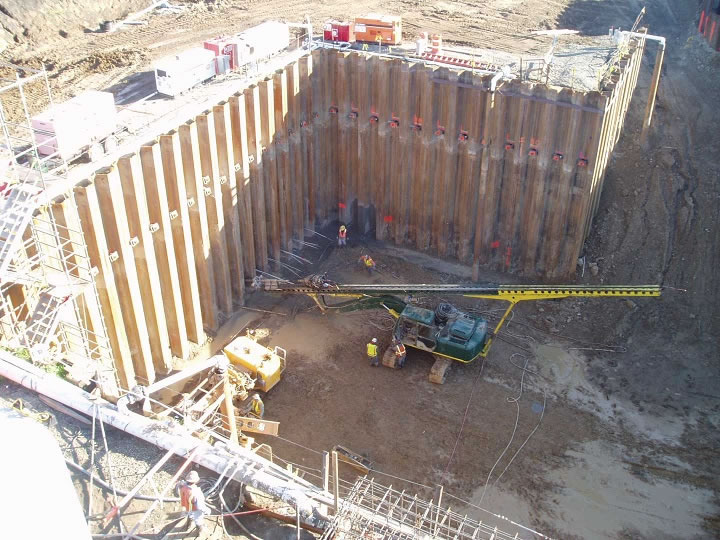
Tablestacas de acero con protección de hormigón
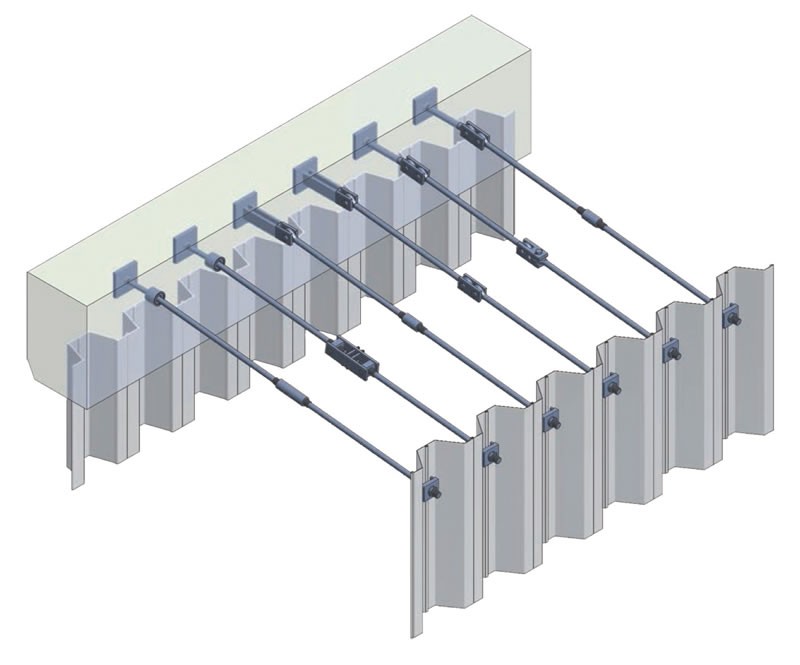
Reparación de tirantes
Pilotes de tubería
La reparación de pilotes de tuberías es generalmente similar a la reparación de pilotes en H Debido a su forma cilíndrica, se protegen más fácilmente con envolturas que otros pilotes.
Componentes de Apoyo
Los componentes de soporte de acero (largueros, tirantes, etc.) deben repararse o reemplazarse, según sea necesario. En la medida de lo posible, deben ubicarse por encima de la línea de agua alta donde la corrosión es menos severa.
Líneas de Utilidad
El objetivo básico es mantener los sistemas de distribución de las empresas de servicios públicos de la manera más económica posible y seguir siendo coherentes con los requisitos operativos, las prácticas de ingeniería sólidas y la protección adecuada de la vida, la salud y la propiedad.
Todas las reparaciones necesarias deben realizarse según lo requiera la inspección periódica. Estas reparaciones pueden requerir el reemplazo de artículos, apretar las conexiones sueltas, apretar o volver a empaquetar el prensaestopas de la válvula y los prensaestopas del sello de conductos, o soldar piezas o secciones defectuosas. Los sistemas de protección catódica deben mantenerse de acuerdo con las instrucciones del fabricante.
En los sistemas de distribución de gas, las tuberías con fugas se reparan cerrando el gas, apretando las conexiones y volviendo a verificar las fugas con espuma de jabón. Cuando se trabaja en sistemas de transmisión y distribución de energía eléctrica, siempre debe haber un asistente disponible para brindar asistencia o primeros auxilios.
Se deben realizar reemplazos extensivos de los sistemas defectuosos de acuerdo con los criterios actuales para construcción.
Accesorios de Amarrre
El mantenimiento de los herrajes de amarre (bitas, bolardos, cornamusas, calzos, etc.) incluye apretar o reemplazar los pernos; reemplazo de accesorios agrietados, rotos o muy corroídos; y refuerzo o reemplazo de cimentaciones.
Las cabezas de los pernos expuestas a la atmósfera deben protegerse de la corrosión rellenando los orificios de los pernos con plomo vertido o con una masilla epoxi.
Los accesorios nuevos deben ser de acero fundido y tener al menos el mismo tamaño y capacidad que los que reemplazan. Deben pintarse con alquitrán de hulla.
Estructuras Flotantes
La reparación de los agujeros en los costados de las estructuras flotantes, los elevadores y los camellos, debe realizarse soldando placas de acero. Las placas deben ser redondeadas y la soldadura lo más suave posible para evitar condiciones que aceleren la corrosión.
El parche temporal se puede hacer atornillando las placas sobre los orificios o con masilla epoxi si la soldadura de las placas requiere un dique seco. La protección catódica protegerá el acero subacuático de la corrosión y se deben utilizar revestimientos protectores sobre el agua.
Debido a su resistencia al impacto y al daño por abrasión y a la corrosión, los recubrimientos inorgánicos de zinc se recomiendan para plataformas de trabajo de acero en barcazas y grúas.
Mantenimiento de Herrajes de Amarre
Los accesorios de amarre incluyen bitas, bolardos, cornamusas y reloj. Su mantenimiento incluye apretar o reemplazar pernos, reemplazar accesorios agrietados, rotos o corroídos. El reemplazo y refuerzo de los cimientos también es parte del mantenimiento de los accesorios de amarre. Los accesorios nuevos deben ser de acero fundido y del mismo tamaño y capacidad que los reemplazados. Deben pintarse con alquitrán de hulla.
Somos un equipo de fabricantes de metales profesionales. Nuestro equipo está capacitado para manejar todos sus requisitos de fabricación. Ponte en contacto con nosotros para conocer más sobre nuestros servicios.
El mantenimiento de estructuras y componentes de acero es crucial para garantizar su durabilidad, seguridad y funcionalidad a lo largo del tiempo. Este proceso no solo previene fallos catastróficos y costosas reparaciones, sino que también extiende significativamente la vida útil de la inversión inicial en la construcción.
Profundizando en el Mantenimiento de Estructuras de Acero
El artículo original proporciona una buena introducción, pero podemos expandir significativamente cada aspecto para ofrecer una guía completa y detallada.
1. Inspección Detallada: Más Allá de lo Visible
La inspección es la piedra angular de cualquier programa de mantenimiento efectivo. No se trata solo de buscar signos evidentes de corrosión; una inspección exhaustiva implica:
- Inspección Visual Avanzada: Uso de herramientas como lupas, endoscopios (para áreas de difícil acceso) y drones equipados con cámaras de alta resolución para inspeccionar grandes estructuras o áreas elevadas. Se buscan no solo óxido, sino también deformaciones, grietas (incluso microscópicas), pandeo, conexiones sueltas o dañadas, y cualquier signo de fatiga del material.
- Mediciones Precisas: Se utilizan calibradores, micrómetros y medidores de espesor ultrasónicos para cuantificar la pérdida de material debido a la corrosión. Esto es fundamental para evaluar la capacidad de carga restante de la estructura.
- Ensayos No Destructivos (END):
- Ultrasonido: Detecta discontinuidades internas, como grietas o inclusiones, midiendo la velocidad de propagación de ondas ultrasónicas.
- Partículas Magnéticas: Revela grietas superficiales y subsuperficiales en materiales ferromagnéticos. Se aplica un campo magnético y se espolvorean partículas ferromagnéticas finas que se acumulan en las discontinuidades.
- Líquidos Penetrantes: Detecta grietas abiertas a la superficie. Se aplica un líquido penetrante que se introduce en las fisuras, luego se remueve el exceso y se aplica un revelador que "extrae" el líquido atrapado, haciéndolo visible.
- Radiografía Industrial: Utiliza rayos X o gamma para obtener imágenes internas de la estructura, revelando defectos internos como porosidad, inclusiones o grietas.
- Termografía Infrarroja: Detecta variaciones de temperatura que pueden indicar corrosión bajo la superficie, delaminaciones o conexiones defectuosas que generan calor por resistencia eléctrica.
- Análisis de Vibraciones: Especialmente útil en puentes y estructuras sometidas a cargas dinámicas. Las vibraciones anormales pueden indicar problemas de rigidez o conexiones sueltas.
- Monitoreo Continuo con Sensores: Instalación de sensores (galgas extensiométricas, acelerómetros, sensores de corrosión, etc.) para monitorear continuamente el estado de la estructura y detectar cambios a lo largo del tiempo. Estos datos se pueden analizar mediante algoritmos de aprendizaje automático para predecir fallos potenciales.
Tipo de Ensayo No Destructivo | Aplicación Principal | Ventajas | Limitaciones |
---|---|---|---|
Ultrasonido | Detección de grietas internas y medición de espesores | Rápido, portátil, relativamente económico | Requiere contacto con la superficie, interpretación por personal capacitado |
Partículas Magnéticas | Detección de grietas superficiales y subsuperficiales en materiales ferromagnéticos | Alta sensibilidad, relativamente simple de aplicar | Solo aplicable a materiales ferromagnéticos, requiere limpieza previa |
Líquidos Penetrantes | Detección de grietas abiertas a la superficie | Aplicable a una amplia variedad de materiales, bajo costo | Solo detecta grietas abiertas a la superficie, requiere limpieza previa y posterior |
Radiografía Industrial | Obtención de imágenes internas de la estructura | Detecta defectos internos, proporciona un registro permanente | Alto costo, requiere precauciones de seguridad radiológica, interpretación por personal especializado |
2. Limpieza Exhaustiva: Preparación para el Éxito
La limpieza es mucho más que una cuestión estética. Es un paso fundamental para asegurar la adherencia de los recubrimientos protectores y para permitir una inspección visual adecuada. Se debe considerar:
- Métodos de Limpieza Avanzados:
- Chorro Abrasivo: Uso de arena, granalla de acero, óxido de aluminio u otros abrasivos proyectados a alta velocidad para eliminar óxido, pintura vieja y contaminantes. Se debe seleccionar el abrasivo adecuado según el grado de limpieza requerido y el tipo de acero. Es crucial controlar la presión y el ángulo del chorro para evitar daños al sustrato.
- Limpieza con Agua a Alta Presión (Hidrolavado): Utiliza agua a presiones extremadamente altas (hasta 40,000 psi o más) para eliminar suciedad, sales, contaminantes y recubrimientos sueltos. Puede combinarse con abrasivos (hidroarenado) para una limpieza más agresiva.
- Limpieza con Láser: Una técnica emergente que utiliza pulsos láser de alta energía para eliminar óxido, pintura y contaminantes sin dañar el sustrato. Es precisa, no genera residuos abrasivos y puede ser automatizada.
- Limpieza Criogénica: Utiliza pellets de hielo seco (CO2 sólido) que se subliman al impactar la superficie, creando un efecto de microexplosiones que eliminan los contaminantes. Es un método no abrasivo y no genera residuos secundarios.
- Limpieza Química: Uso de soluciones ácidas, alcalinas o solventes para disolver o eliminar contaminantes específicos. Requiere un manejo cuidadoso y la neutralización adecuada de los residuos. Es crucial seleccionar el producto químico apropiado para el tipo de contaminante y el tipo de acero, evitando reacciones adversas.
- Preparación de la Superficie: Después de la limpieza, la superficie debe ser tratada para mejorar la adherencia del recubrimiento. Esto puede incluir:
- Perfil de Anclaje: Creación de una rugosidad microscópica en la superficie mediante chorro abrasivo o herramientas mecánicas. Esto proporciona una mayor área de contacto para el recubrimiento y mejora su adherencia mecánica.
- Aplicación de Imprimantes: Capas delgadas de pintura que se aplican antes del recubrimiento principal. Los imprimantes mejoran la adherencia, proporcionan protección anticorrosiva adicional y pueden actuar como barrera entre el acero y el recubrimiento.
- Consideraciones Ambientales: La limpieza, especialmente con chorro abrasivo, puede generar polvo y residuos que deben ser contenidos y eliminados de manera segura para proteger el medio ambiente y la salud de los trabajadores. Se deben utilizar sistemas de recolección de polvo, barreras de contención y equipos de protección personal adecuados.
Método de Limpieza | Aplicaciones | Ventajas | Desventajas |
---|---|---|---|
Chorro Abrasivo | Eliminación de óxido, pintura vieja, y preparación de superficies | Efectivo, versátil, crea perfil de anclaje | Genera polvo, requiere equipo especializado, puede dañar el sustrato si no se controla adecuadamente |
Hidrolavado | Eliminación de suciedad, sales y contaminantes | Rápido, no genera polvo, puede usarse en áreas sensibles | Menos efectivo para eliminar óxido y pintura fuertemente adherida, puede requerir grandes volúmenes de agua |
Limpieza Química | Eliminación de contaminantes específicos, preparación de superficies | Puede ser muy efectivo para ciertos contaminantes, puede ser menos agresivo que el chorro abrasivo | Requiere manejo cuidadoso de productos químicos, puede generar residuos peligrosos, puede dañar el sustrato si no se selecciona adecuadamente |
3. Reparación y Refuerzo: Restaurando la Integridad Estructural
Las reparaciones no se limitan a soldar grietas. Se deben abordar todos los problemas identificados durante la inspección, y en muchos casos, se requiere un análisis de ingeniería para determinar la mejor solución:
- Reparación de Grietas:
- Soldadura: La técnica más común. Se debe seleccionar el procedimiento de soldadura adecuado (SMAW, GMAW, FCAW, GTAW) y los materiales de aporte compatibles con el acero base. Es crucial realizar una preparación adecuada de la junta (biselado, limpieza) y controlar los parámetros de soldadura (amperaje, voltaje, velocidad) para evitar defectos como porosidad, falta de fusión o grietas inducidas por el calor.
Es fundamental realizar una inspección posterior a la soldadura (visual, radiografía, ultrasonido) para verificar la calidad de la reparación. - Refuerzo con Placas: En algunos casos, se pueden atornillar o soldar placas de acero adicionales para reforzar la zona afectada por la grieta. Esto distribuye la carga y reduce la concentración de tensiones.
- Soldadura: La técnica más común. Se debe seleccionar el procedimiento de soldadura adecuado (SMAW, GMAW, FCAW, GTAW) y los materiales de aporte compatibles con el acero base. Es crucial realizar una preparación adecuada de la junta (biselado, limpieza) y controlar los parámetros de soldadura (amperaje, voltaje, velocidad) para evitar defectos como porosidad, falta de fusión o grietas inducidas por el calor.
- Reemplazo de Elementos Dañados: Si un elemento está severamente corroído o deformado, puede ser necesario reemplazarlo por completo. Esto requiere un diseño cuidadoso para asegurar que el nuevo elemento se integre adecuadamente con la estructura existente y cumpla con los requisitos de carga.
- Refuerzo de Conexiones: Las conexiones (tornillos, soldaduras, remaches) son puntos críticos en una estructura. Si se encuentran sueltas, corroídas o dañadas, deben ser reparadas o reforzadas. Esto puede implicar:
- Reapriete de Tornillos: Utilizando una llave dinamométrica para asegurar el torque adecuado.
- Reemplazo de Tornillos o Remaches: Utilizando elementos del mismo tipo y grado, o de mayor resistencia si es necesario.
- Adición de Soldadura: Para reforzar conexiones existentes o crear nuevas conexiones.
- Uso de Adhesivos Estructurales: En combinación a las uniones mecánicas, en algunos casos.
- Refuerzo Estructural: Si el análisis de ingeniería revela que la estructura ha perdido capacidad de carga debido a la corrosión o a otros factores, puede ser necesario reforzarla. Esto puede implicar:
- Adición de Elementos de Refuerzo: Vigas, columnas, diagonales, etc.
- Encamisado de Elementos: Rodear un elemento existente con una capa de concreto reforzado o acero.
- Postensado: Introducir tensiones en la estructura mediante cables de acero de alta resistencia.
- Análisis Estructural Detallado: Antes de cualquier reparación o refuerzo significativo, se debe realizar un análisis estructural detallado utilizando software de elementos finitos (FEA) para evaluar el impacto de las modificaciones en la capacidad de carga y la estabilidad de la estructura.
4. Protección Contra la Corrosión: La Clave de la Longevidad
La corrosión es el principal enemigo de las estructuras de acero. La protección contra la corrosión es un proceso continuo que va más allá de la simple aplicación de pintura:
- Selección del Sistema de Protección: La elección del sistema de protección adecuado depende de varios factores:
- Ambiente: El nivel de exposición a la humedad, la salinidad, los contaminantes industriales, la radiación UV, etc.
- Tipo de Acero: Algunos aceros son más resistentes a la corrosión que otros (por ejemplo, aceros inoxidables o aceros con aleaciones especiales).
- Vida Útil Deseada: El tiempo que se espera que la estructura permanezca en servicio.
- Costo: El presupuesto disponible para el mantenimiento.
- Estética: En estructuras visibles, la apariencia del recubrimiento puede ser un factor importante.
- Accesibilidad: Algunos sistemas de protección son más fáciles de aplicar y mantener en áreas de difícil acceso.
- Tipos de Protección:
- Recubrimientos Orgánicos (Pinturas): La forma más común de protección. Existen diferentes tipos de pinturas:
- Epoxis: Excelente resistencia a la corrosión, la abrasión y los productos químicos.
- Poliuretanos: Buena resistencia a la intemperie y a la radiación UV.
- Alquídicos: Menor costo, pero menor durabilidad que los epoxis y poliuretanos.
- Ricos en Zinc: Proporcionan protección catódica al acero, sacrificándose a sí mismos para protegerlo.
- Intumescentes: Protección pasiva contra incendios.
Los sistemas de pintura suelen consistir en varias capas: imprimante, capa intermedia y capa de acabado. Cada capa tiene una función específica (adherencia, barrera, resistencia a la intemperie, etc.). El espesor total del recubrimiento es crucial para su durabilidad.
- Recubrimientos Metálicos:
- Galvanizado en Caliente: Inmersión del acero en zinc fundido para crear una capa protectora. Proporciona protección catódica y una barrera física.
- Metalización: Proyección de metal fundido (zinc, aluminio, etc.) sobre la superficie del acero. Puede aplicarse en campo y permite recubrir grandes áreas.
- Protección Catódica: Utiliza una corriente eléctrica para prevenir la corrosión. Puede ser:
- Ánodos de Sacrificio: Se conectan piezas de un metal más activo (zinc, magnesio, aluminio) al acero. Estos ánodos se corroen preferentemente, protegiendo el acero.
- Corriente Impresa: Se utiliza una fuente de corriente continua para suministrar electrones al acero, haciéndolo catódico y previniendo la corrosión.
La protección catódica es especialmente útil en estructuras enterradas o sumergidas, o en ambientes muy agresivos.
- Inhibidores de Corrosión: Sustancias químicas que se añaden al ambiente (por ejemplo, al agua de refrigeración) o se aplican directamente sobre el acero para reducir la velocidad de corrosión.
- Recubrimientos Orgánicos (Pinturas): La forma más común de protección. Existen diferentes tipos de pinturas:
- Aplicación y Control de Calidad: La aplicación del sistema de protección debe ser realizada por personal cualificado y siguiendo las especificaciones del fabricante. Se deben controlar factores como la preparación de la superficie, el espesor del recubrimiento, el tiempo de secado entre capas y las condiciones ambientales (temperatura, humedad). Se deben realizar inspecciones y pruebas para verificar la calidad del recubrimiento (adherencia, espesor, porosidad).
- Mantenimiento de los Recubrimientos: Los recubrimientos protectores se degradan con el tiempo debido a la exposición a los elementos. Es necesario realizar inspecciones periódicas y retoques o reparaciones localizadas para mantener la integridad del recubrimiento. En algún momento, será necesario repintar o reaplicar el recubrimiento por completo.
Tipo de Protección | Mecanismo de Protección | Ventajas | Desventajas |
---|---|---|---|
Pintura Epoxi | Barrera física, resistencia química | Versátil, buena adherencia, resistente a la abrasión | Requiere preparación de superficie, puede ser sensible a la radiación UV |
Galvanizado en Caliente | Barrera física, protección catódica | Larga duración, buena resistencia a la abrasión | Solo aplicable en fábrica, puede ser difícil de reparar |
Protección Catódica (Ánodos de Sacrificio) | Protección electroquímica | Efectiva en ambientes agresivos, relativamente fácil de instalar | Requiere reemplazo periódico de los ánodos, no proporciona una barrera física |
5. Mantenimiento Preventivo vs. Correctivo vs Predictivo: Un Enfoque Estratégico
El mantenimiento de estructuras de acero no debe ser reactivo (solo actuar cuando hay un problema). Un enfoque estratégico implica una combinación de diferentes tipos de mantenimiento:
- Mantenimiento Preventivo: Acciones planificadas y programadas para prevenir fallos y prolongar la vida útil de la estructura. Incluye inspecciones regulares, limpieza, lubricación de elementos móviles, reapriete de tornillos, retoque de pintura, etc. El mantenimiento preventivo es más económico que el correctivo, ya que evita reparaciones mayores y paradas no programadas.
- Mantenimiento Correctivo: Acciones realizadas para reparar un fallo o defecto que ya ha ocurrido. Incluye soldadura de grietas, reemplazo de elementos dañados, reparación de conexiones, etc. El mantenimiento correctivo es más costoso que el preventivo y puede implicar interrupciones en el uso de la estructura.
- Mantenimiento Predictivo: Utiliza técnicas de monitoreo y análisis de datos para predecir cuándo ocurrirá un fallo y programar el mantenimiento antes de que ocurra. Incluye análisis de vibraciones, termografía infrarroja, monitoreo con sensores, análisis de aceite (en equipos mecánicos), etc. El mantenimiento predictivo es el enfoque más avanzado y puede optimizar los costos de mantenimiento al evitar intervenciones innecesarias y programar el mantenimiento en el momento óptimo.
- Mantenimiento Basado en la Condición (CBM): Es una forma de mantenimiento predictivo que se basa en la monitorización continua del estado de la estructura o equipo utilizando sensores y sistemas de adquisición de datos. Los datos recopilados se analizan en tiempo real para detectar cambios que indiquen un deterioro o una posible falla. El CBM permite tomar decisiones de mantenimiento basadas en la condición real del activo, en lugar de seguir un programa fijo o reaccionar a una falla.
6. Documentación y Registro: La Memoria Institucional
Un programa de mantenimiento eficaz debe incluir una documentación completa y detallada de todas las actividades realizadas:
- Historial de la Estructura: Información sobre el diseño original, los materiales utilizados, las cargas de diseño, los planos de construcción, las modificaciones realizadas, etc.
- Plan de Mantenimiento: Un documento que describe las tareas de mantenimiento a realizar, la frecuencia, los procedimientos, los materiales y equipos necesarios, y los responsables de cada tarea.
- Informes de Inspección: Registros detallados de todas las inspecciones realizadas, incluyendo la fecha, el inspector, los hallazgos, las fotografías, los resultados de los ensayos no destructivos, etc.
- Registros de Mantenimiento: Documentación de todas las tareas de mantenimiento realizadas (limpieza, reparaciones, reemplazos, aplicación de recubrimientos, etc.), incluyendo la fecha, el personal involucrado, los materiales utilizados, los costos, etc.
- Análisis de Fallos: Si ocurre un fallo, se debe realizar un análisis para determinar la causa raíz y tomar medidas para evitar que se repita. Este análisis debe ser documentado.
- Software de Gestión de Mantenimiento Asistido por Computadora (CMMS): Utilizar un software especializado para gestionar el programa de mantenimiento. Estos sistemas permiten programar tareas, generar órdenes de trabajo, llevar un registro de los costos, gestionar el inventario de repuestos, generar informes, etc. Facilitan enormemente la planificación, ejecución y seguimiento del mantenimiento.
La documentación es fundamental para asegurar la trazabilidad de las actividades de mantenimiento, para evaluar la efectividad del programa de mantenimiento, para tomar decisiones informadas sobre futuras intervenciones y para cumplir con los requisitos normativos.
Reparación y Rehabilitación de Estructuras
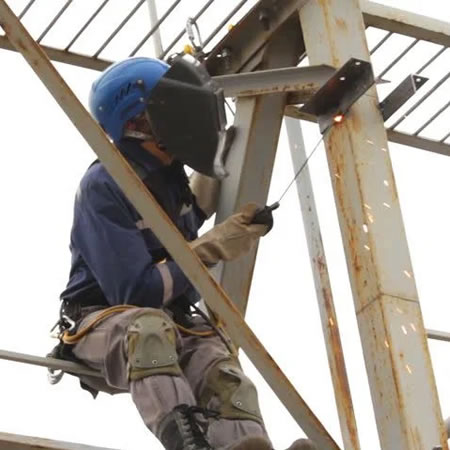
Estrategias de mantenimiento y arreglo
Las actividades incluyen inspección y trabajos necesarios para cumplir con la función prevista o para mantener el estándar de servicio original.
Leer másMantenimiento de Edificaciones: Significado, Objetivos y Tipos
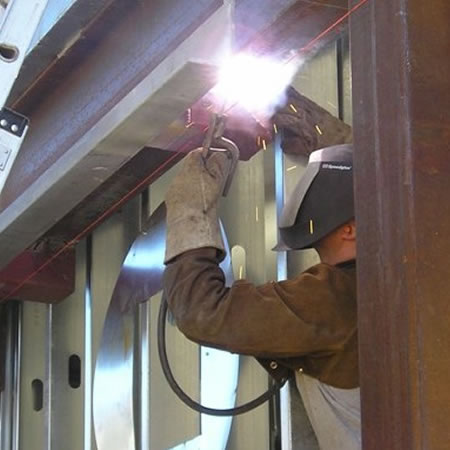
Objetivo del mantenimiento de una edificación
El mantenimiento de rutina de la estructura es esencial para mantenerla funcional y protegerla contra el deterioro temprano.
Leer másEnfoques metódicos para reparar edificaciones
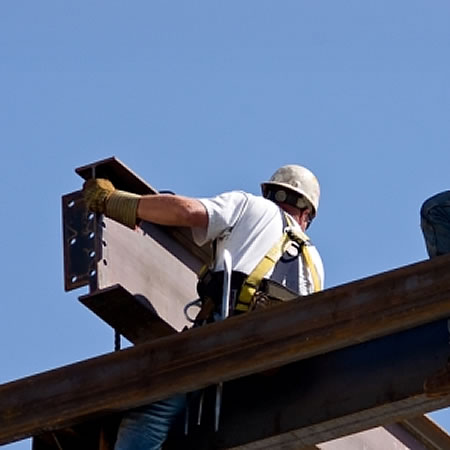
Las reparaciones en estructuras deben realizarse de manera metódica.
El primer paso en esta dirección sería la inspección de la construcción para determinar el alcance del daño y también los elementos de daño y deterioro.
Leer másSignificado y causas del deterioro en Edificaciones
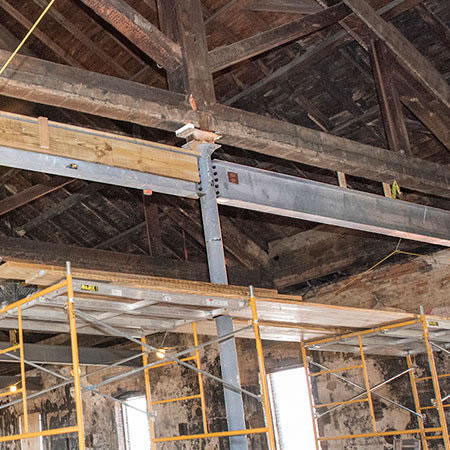
Rehabilitación de una estructura ruinosa
Una estructura ruinosa propuesta para rehabilitación necesita ser examinado a fondo, especialmente sus miembros estructurales.
Leer másCerchas en Construcciones Metálicas
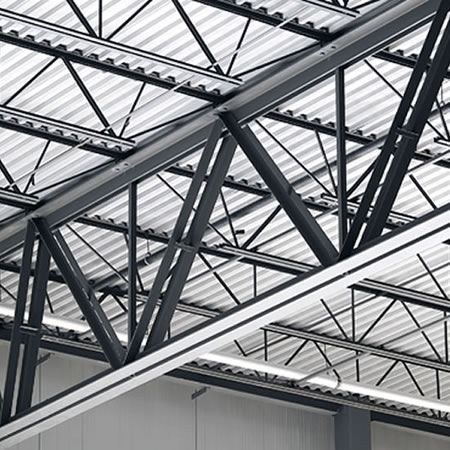
Diferentes formas y consideraciones de diseño para cerchas
Una cercha es esencialmente un sistema triangulado de elementos estructurales interconectados rectos.
Leer másConstrucción de Pórticos
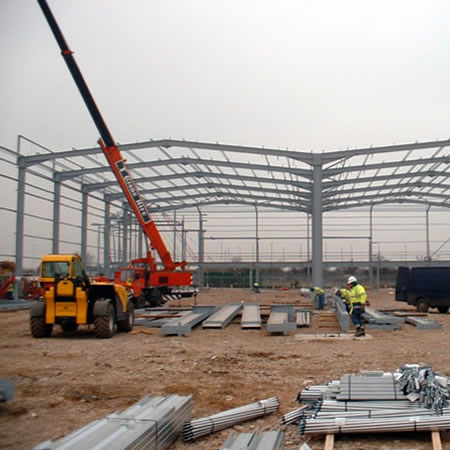
Diseño, construcción y levantamiento de marcos estructurales para PÓRTICOS
Los Pórticos o tambien llamados "marcos de portal" son generalmente estructuras de poca altura, que comprenden columnas y vigas horizontales o inclinadas, conectadas por conexiones resistentes al momento.
Leer másPórticos con Estructura de Espacio Abierto
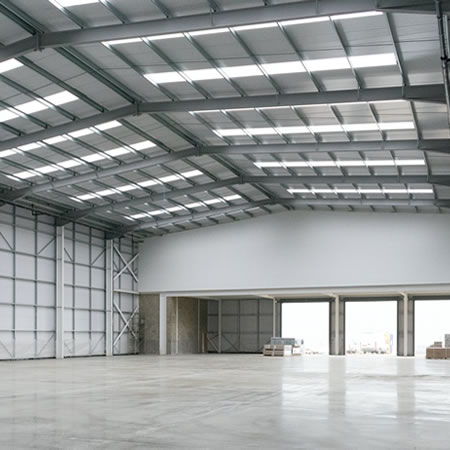
¿Qué es un espacio despejado o pórtico de un amplio tramo claro?
La construcción de un amplio tramo claro están diseñada como un marco rígido que tiene alta resistencia y durabilidad.
Leer más¿Marcos rígidos de un solo tramo o varios tamos?
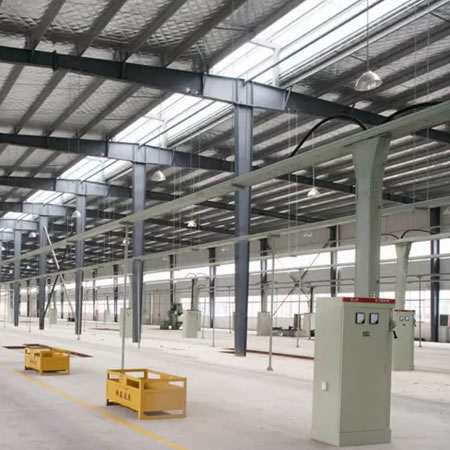
¿Qué se entiende por Construcción de Marco Rígido?
La construcción de marco rígido también se denomina construcción de marco fijo o resistente a momentos.
Leer más